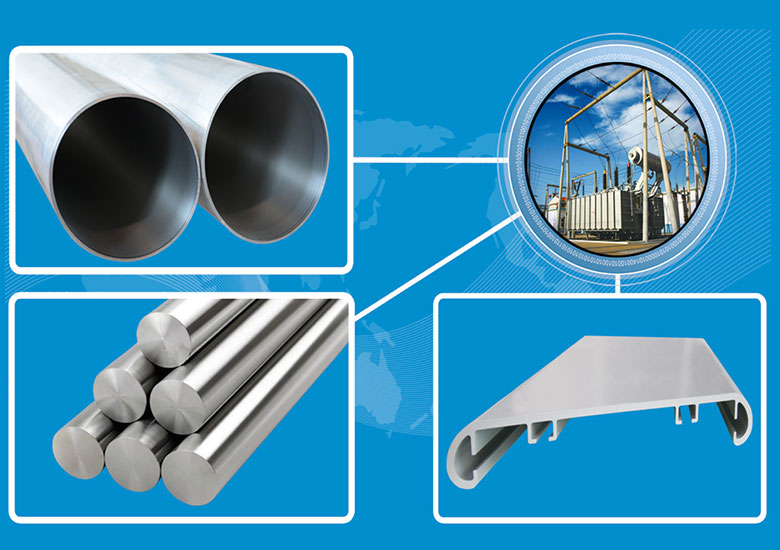
Aluminum Bus Bar Extrusion
Aluminum bus bar extrusion is a manufacturing process used to create long, continuous lengths of aluminum bus bars with a specific cross-sectional profile. It is a cost-effective and efficient method for producing these essential components in the electrical power distribution industry. Aluminum bus bar extrusion plays a crucial role in the efficient and cost-effective production of these essential electrical conductors, enabling various applications across diverse industries.
Raw Material: Aluminum Alloy 6063,6101,6005A etc.
Aluminum Bus Bar Extrusion Process:
1. Billet preparation: The process begins with an aluminum billet, a cylindrical or rectangular block of raw aluminum. The billet is preheated to a specific temperature, making it more malleable for the extrusion process.
2. Extrusion press: The preheated billet is then loaded into a powerful extrusion press. This press uses a ram to apply immense pressure on the billet, forcing it through a die with the desired cross-sectional shape for the bus bar.
3. Shaping the bus bar: The die essentially acts as a mold, shaping the softened aluminum as it passes through. The emerging aluminum takes on the profile of the die cavity, forming the lengthy bus bar with the required dimensions and shape.
4. Cooling and finishing: The extruded bus bar then undergoes cooling to solidify the aluminum. Depending on the specific application and desired properties, the bus bar might go through additional finishing processes such as straightening, cutting to specific lengths, or surface treatments like anodizing for enhanced corrosion resistance.
Advantages of Aluminum Bus Bar Extrusion
Cost-effective: Compared to other methods like machining individual bars, extrusion offers a faster and more economical way to produce large quantities of bus bars.
Dimensional accuracy: The extrusion process allows for precise control over the dimensions and cross-sectional profile of the bus bars, ensuring consistency and meeting desired specifications.
Wide range of shapes: Extrusions can be used to create bus bars with various complex shapes, not just simple bars, catering to specific application requirements.
Material efficiency: Extrusion minimizes material waste compared to other methods, making it a more sustainable manufacturing process.
Applications of Aluminum Bus Bar Extrusion
Power distribution: In buildings, factories, and substations, bus bars distribute power from transformers to various electrical loads.
Renewable energy integration: Solar and wind energy installations use bus bars to collect and transmit the generated electricity.
Transportation: Electric vehicles and their charging infrastructure utilize bus bars for efficient power management.
Manufacturing and industrial applications: They are used in control panels and for high-current connections within machinery.