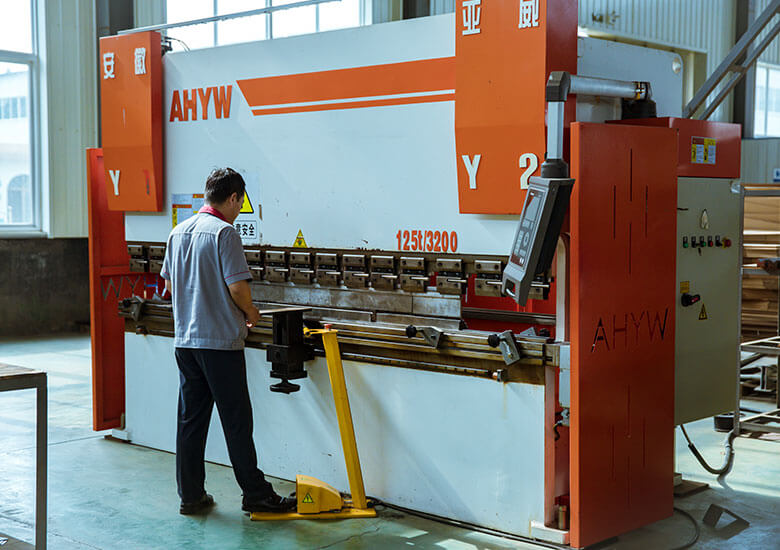
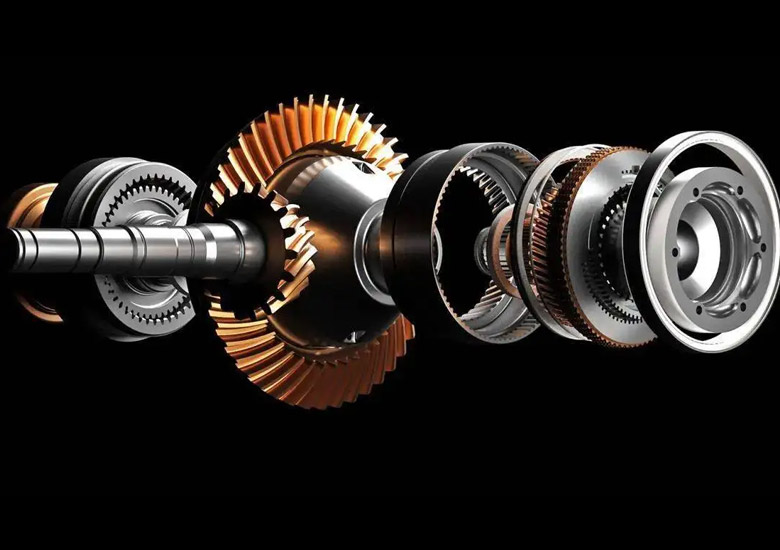
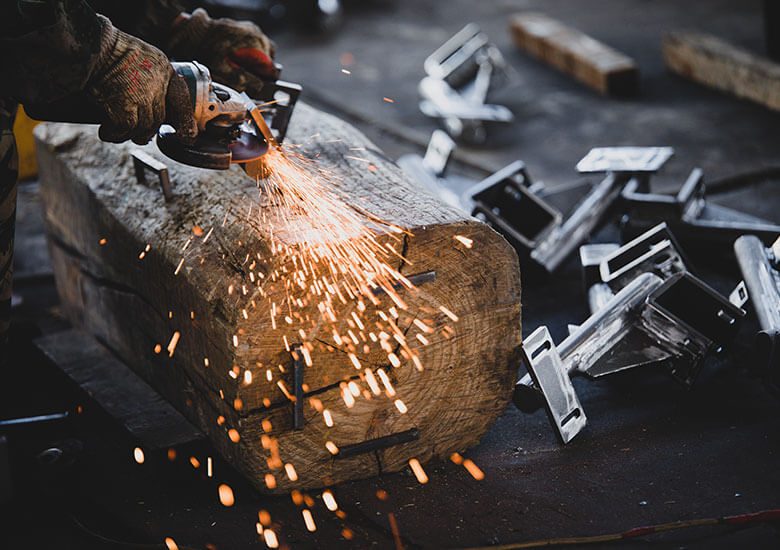
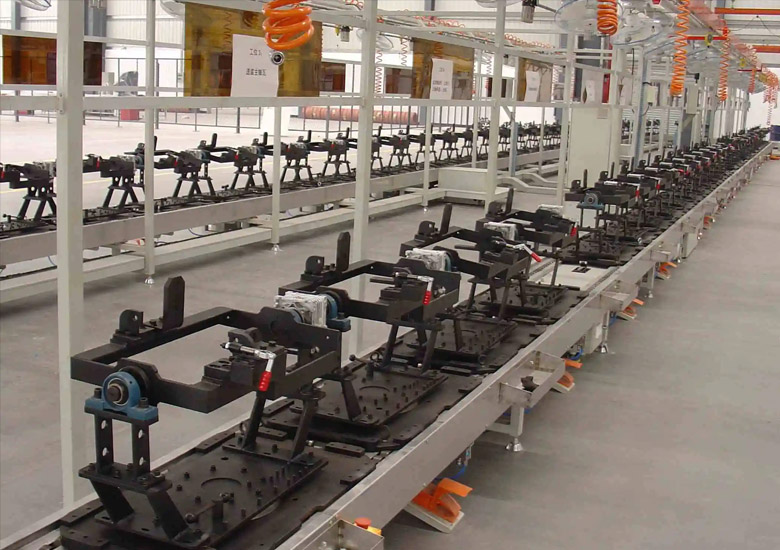
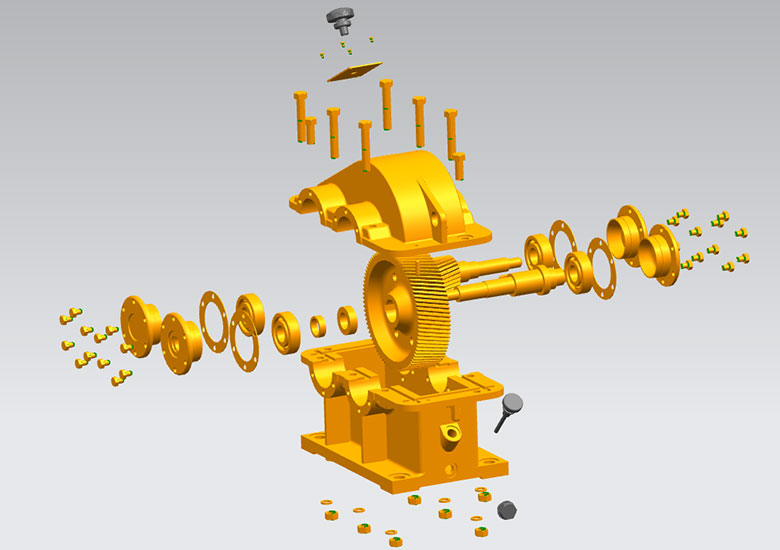
One-stop Service
Custom Malleable Iron Casting Service:
Our company has been providing OEM services for nearly 20 years, and our rich experience can ensure that we provide customers with high-quality one-stop services.
What We Do:
Our Factory
Maxwill is focused on manufacturing high-quality cast iron parts for a variety of industries, including marine castings, municipal casting, constructing products, electrical power fittings, and automobile products.
Our automatic line of clay sand casting has an average capacity of 50 tons per day. We have also retained the original manual molding workshop with an average capacity of 10 tons per day. At the same time, we can manufacture 15 tons of shell casting products per day.
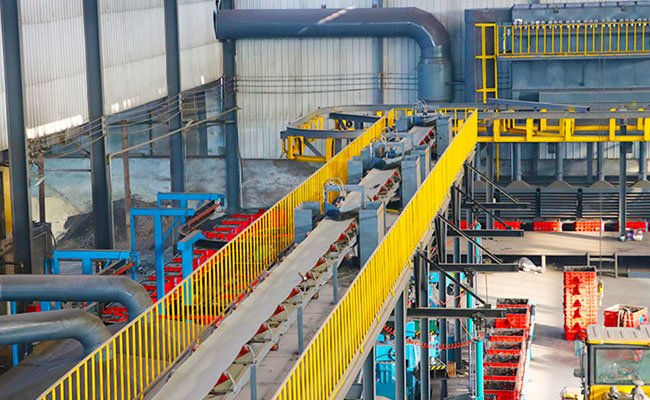
Automatic Line
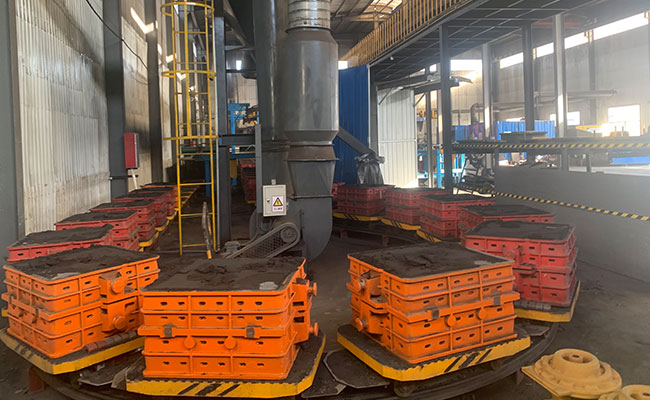
Automatic Line
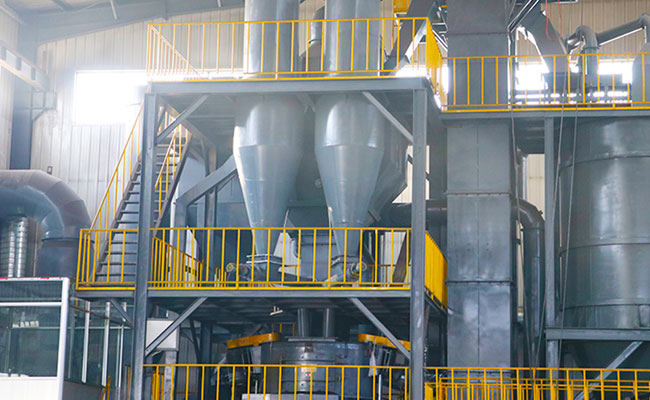
Sand Treatment
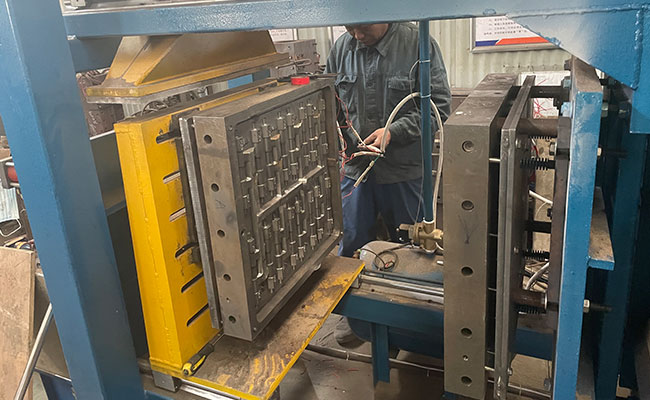
Shell Casting Pattern
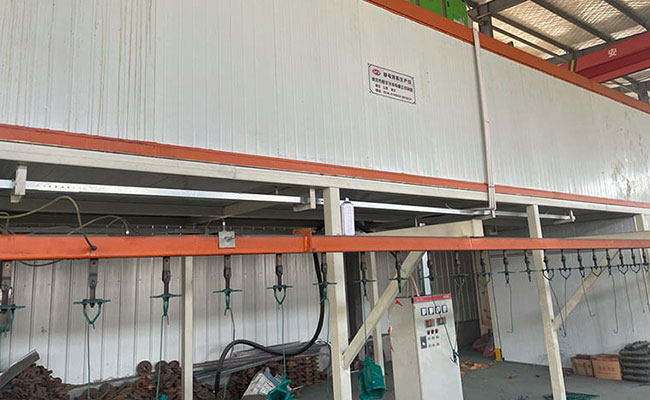
Powder Coating Line
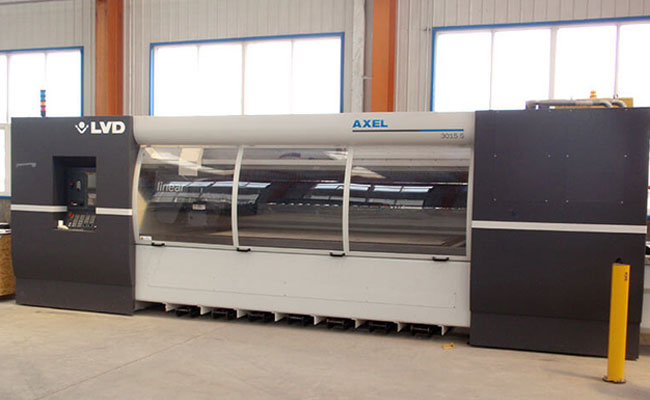
Laser Cutting Machine
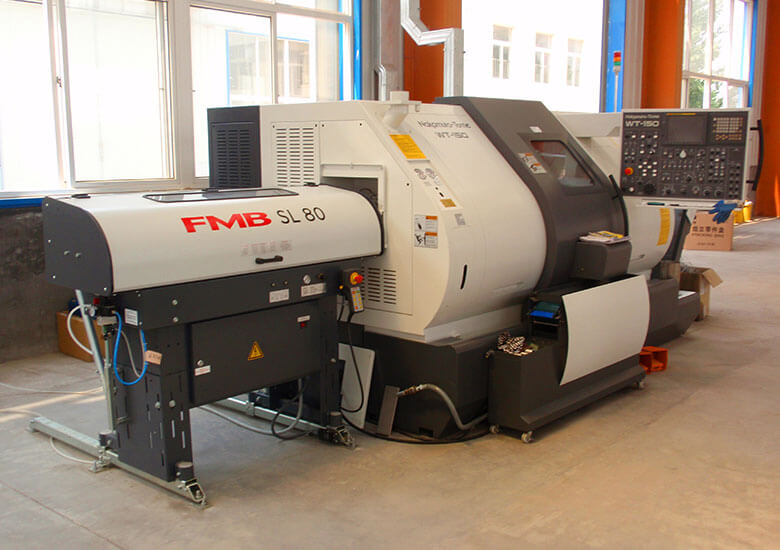
Machining Center
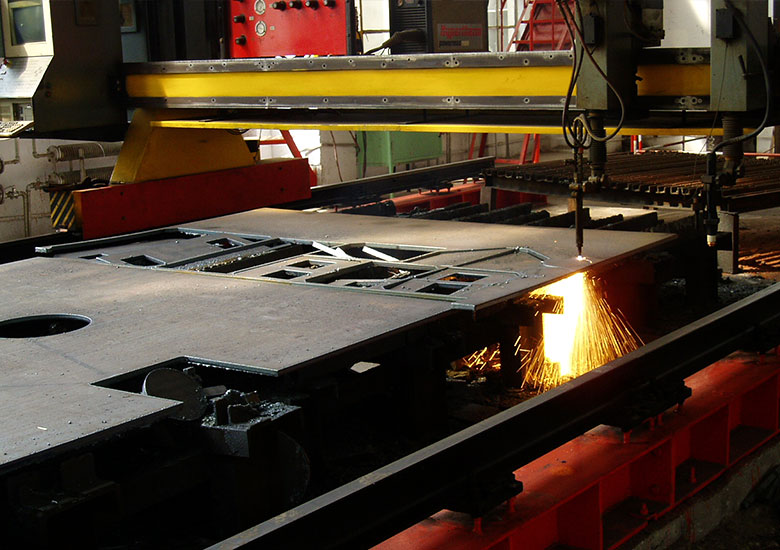
Engraving Machine
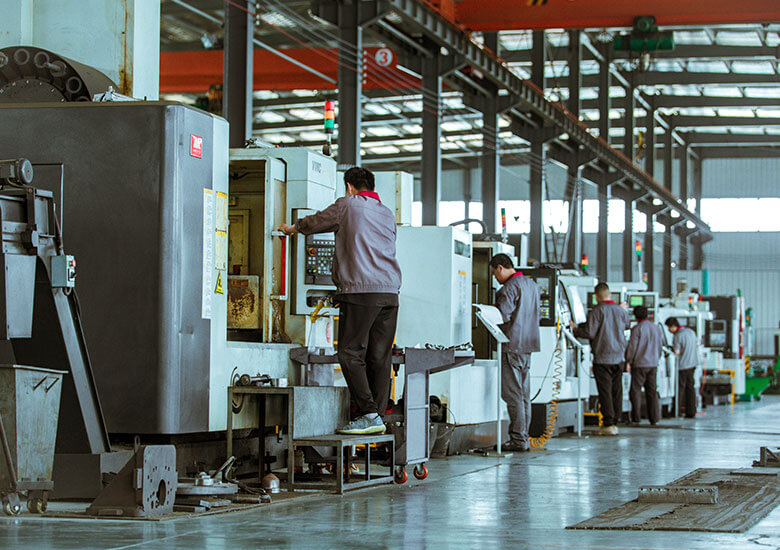
CNC Lathe
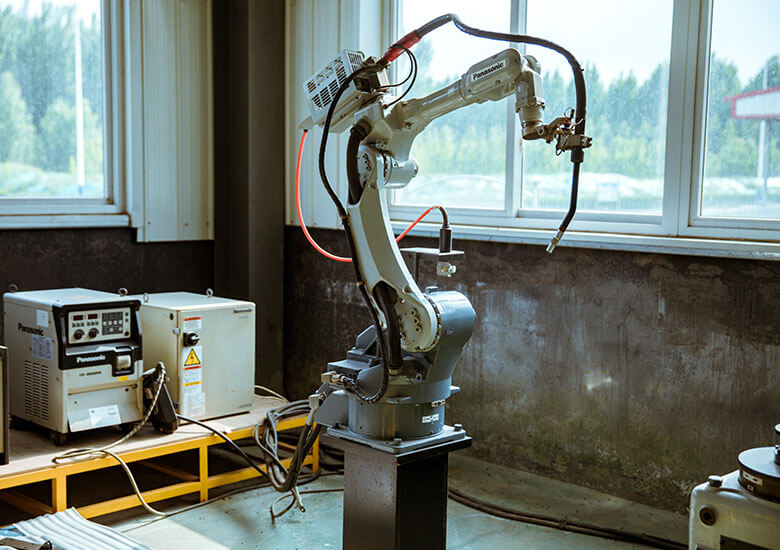
Welding Robot
Quality Control:
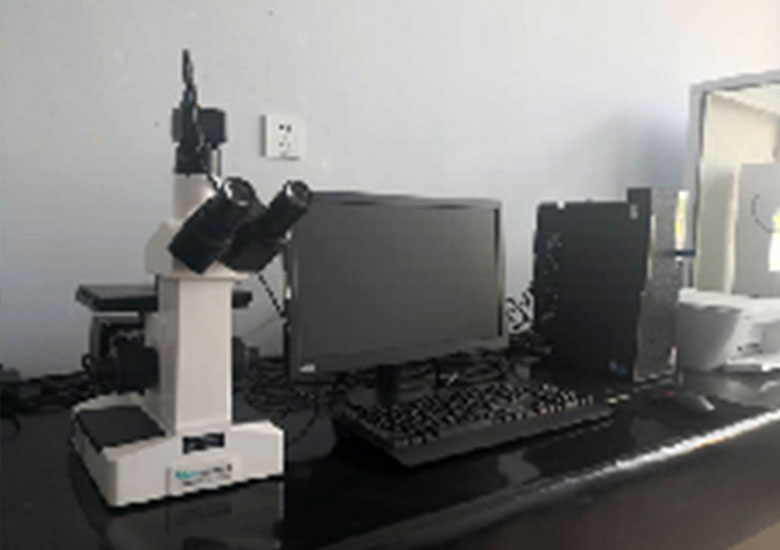
Metallurgical Microscope
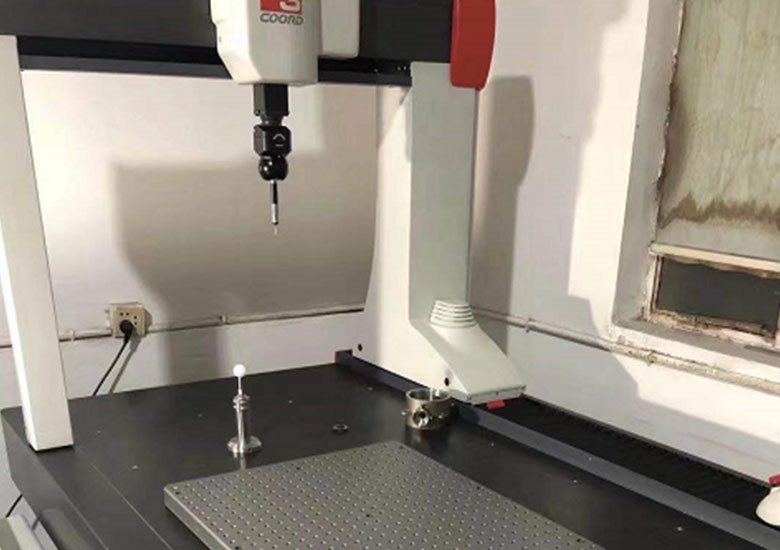
Three Coordinates Measuring Machine
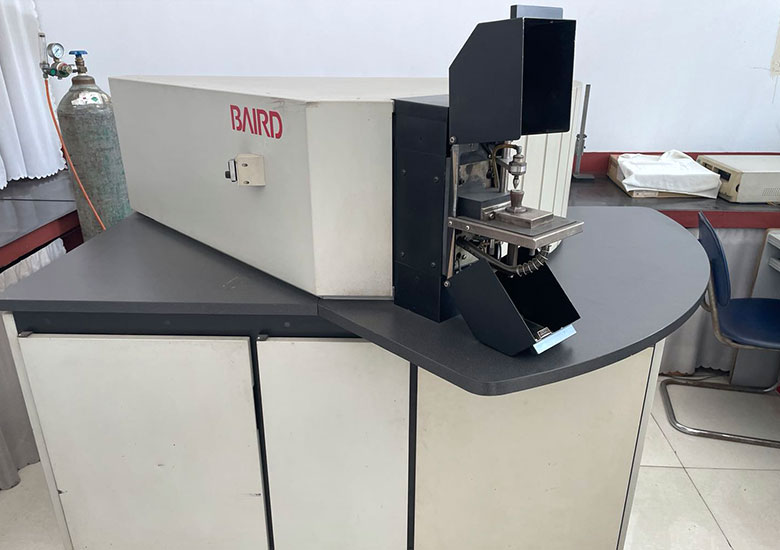
Spectrometer
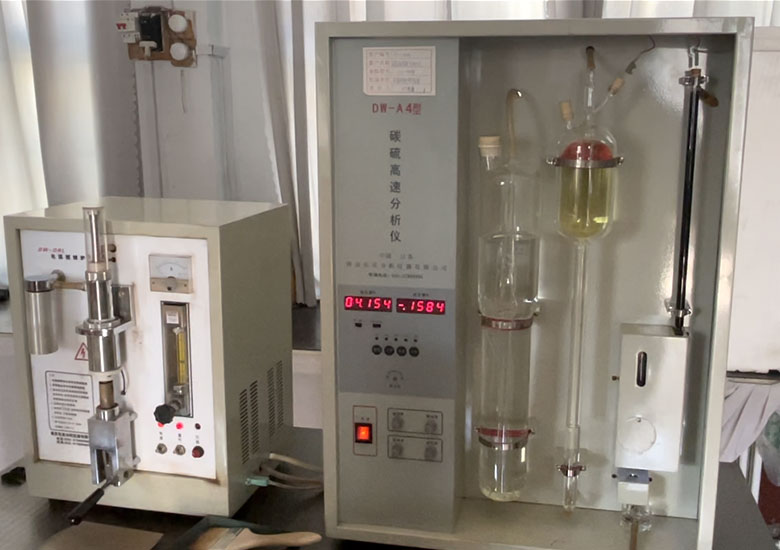
High-speed Carbon and Sulfur Analyzer
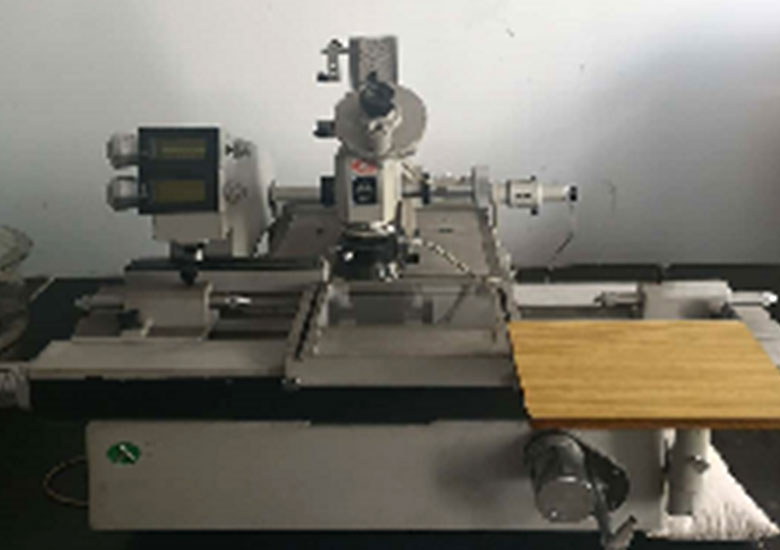
Universal Tool Microscope
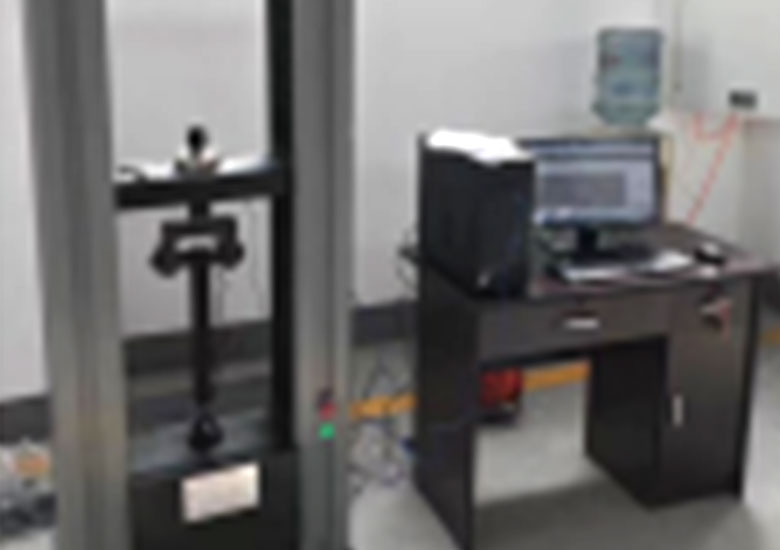
Tensile Testing Machine
How to choose the right metal casting process?
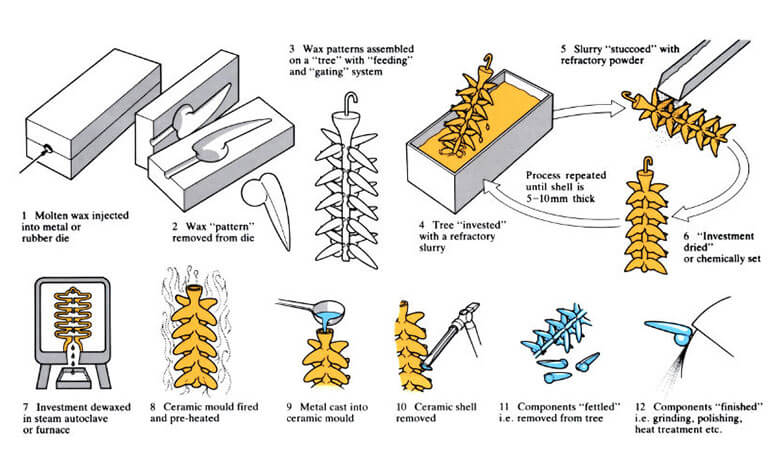
Investment Casting
Investment casting is also called lost wax casting. It is generally used for making complex-shaped components that require tighter tolerances, thinner walls and better surface finish than can be obtained with sand casting.
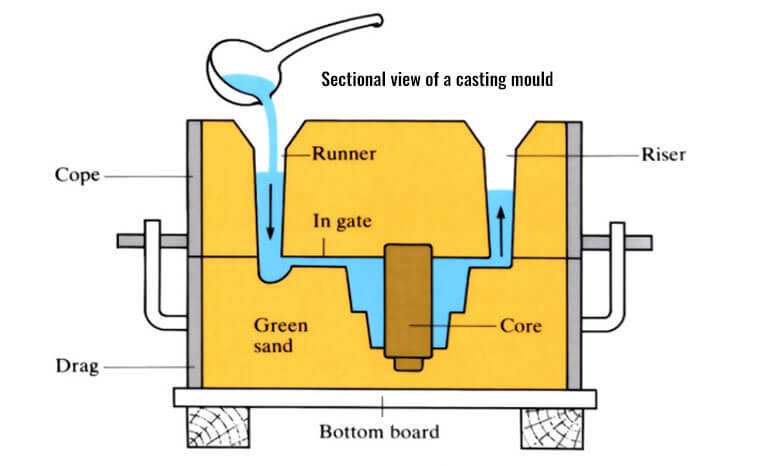
Sand Casting
Sand casting, the most widely used casting process, utilizes expendable sand molds to form complex metal parts that can be made of nearly any alloy. Because the sand mold must be destroyed in order to remove the part, called the casting, sand casting typically has a low production rate. The sand casting process involves the use of a furnace, metal, pattern, and sand mold. The metal is melted in the furnace and then ladled and poured into the cavity of the sand mold, which is formed by the pattern. The sand mold separates along a parting line and the solidified casting can be removed.
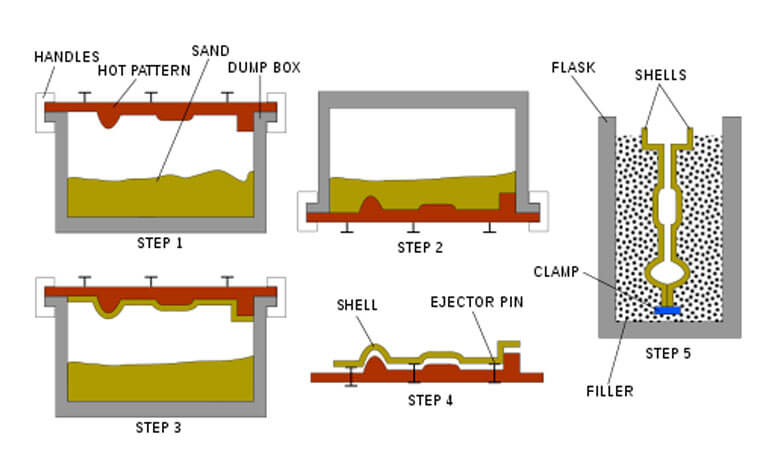
Shell Casting
Shell mold casting is a metal casting process similar to sand casting, in that molten metal is poured into an expendable mold. However, in shell mold casting, the mold is a thin-walled shell created from applying a sand-resin mixture around a pattern. The pattern, a metal piece in the shape of the desired part, is reused to form multiple shell molds. A reusable pattern allows for higher production rates, while the disposable molds enable complex geometries to be cast. Shell mold casting requires the use of a metal pattern, oven, sand-resin mixture, dump box, and molten metal.